In today’s highly competitive market, manufacturing units are constantly seeking ways to increase efficiency, reduce costs, and maintain high product quality. One powerful approach that has proven to transform manufacturing operations is the implementation of Lean principles. Rooted in the Japanese manufacturing philosophy, Lean is centered on the concept of continuous improvement and maximizing value while minimizing waste. Let’s explore how Lean principles can help your manufacturing unit grow.
Waste Reduction (Muda)
The foundation of Lean lies in identifying and eliminating waste (known as muda in Lean terminology). Waste in manufacturing comes in many forms, such as:
– Overproduction
– Unnecessary transportation
– Excess inventory
– Waiting times
– Defects and rework
By implementing Lean practices, your unit can streamline processes, reduce downtime, and minimize waste, thereby reducing costs and improving profitability.
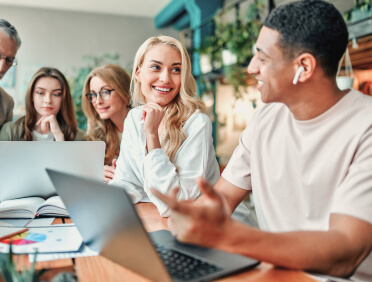
Improved Quality
Lean focuses heavily on delivering quality at every stage of production. This concept, often termed as built-in quality, ensures that defects are identified early in the process, preventing defective products from moving to the next stage. Techniques like Poka-Yoke (mistake-proofing) and Jidoka (automation with human intelligence) enable workers to stop production when an issue arises and solve it immediately. Improved product quality leads to fewer returns, higher customer satisfaction, and increased business growth.
Enhanced Employee Engagement
Faster Production Cycles*
Lean principles such as Just-In-Time (JIT) aim to produce only what is needed, when it is needed, and in the exact quantities required. This results in reduced lead times, less inventory sitting idle, and faster turnaround times for customer orders. A manufacturing unit that can quickly respond to customer demands without compromising quality is more likely to capture a larger market share.
Cost Reduction
Implementing Lean principles can lead to significant cost savings. By eliminating waste, improving quality, and reducing inventory, manufacturing units can lower their operating costs. In addition, Lean encourages preventative maintenance, which helps avoid costly machinery breakdowns and prolongs equipment life.
Flexibility and Scalability
A Lean manufacturing unit is more adaptable to changes in market conditions. Whether there’s a shift in customer demand or the need to introduce a new product line, Lean practices make it easier to scale operations. For instance, Heijunka (production leveling) helps balance workload across the production process, reducing bottlenecks and ensuring consistent output even as demand fluctuates.
Increased Customer Value
At its core, Lean is about delivering value to the customer. By optimizing processes, reducing lead times, and ensuring high-quality products, a Lean manufacturing unit can exceed customer expectations. Satisfied customers are more likely to be loyal and recommend your products, leading to business growth.
Better Decision Making
Lean manufacturing relies heavily on data-driven decision-making. Tools such as Value Stream Mapping and Root Cause Analysis enable leaders to make informed decisions that directly impact production efficiency. With real-time data, managers can respond quickly to issues and implement changes that support growth.
Conclusion
Incorporating Lean principles into your manufacturing unit can lead to substantial improvements in efficiency, cost savings, and customer satisfaction. By focusing on waste reduction, continuous improvement, and employee empowerment, Lean can help your manufacturing unit grow sustainably. Whether you’re just starting out or looking to scale your operations, Lean offers a pathway to operational excellence and long-term success.
By embracing Lean, you’re not just adopting a set of tools but fostering a culture of continuous improvement that will position your manufacturing unit for future growth.