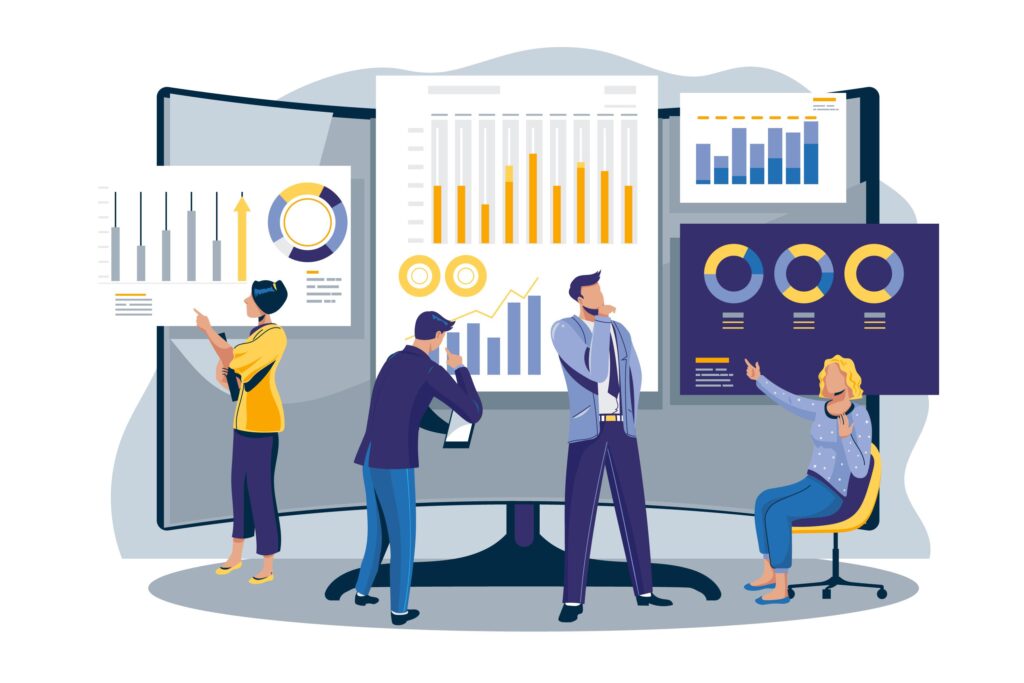
Operations
At Logicate Solution, we focus mainly on operations that we turn into value-driving, cost, and productivity improvement that enable us to come up with distinct operations solutions to enhance your business’s performance and development.
Cost Reduction
Reducing the cost is a prominent aspect of cost management and one that must not come at the cost of the quality of the product. The above cost-reduction services are designed by assessing your expenditures to establish where cuts can be made. Another is the managerial operation where we create and employ different plans that help to minimize costs within the purchase, manufacturing, and administrative expense departments. Organizations should thus strive to contain costs in sustainable ways and at the same time uphold quality and efficiency.
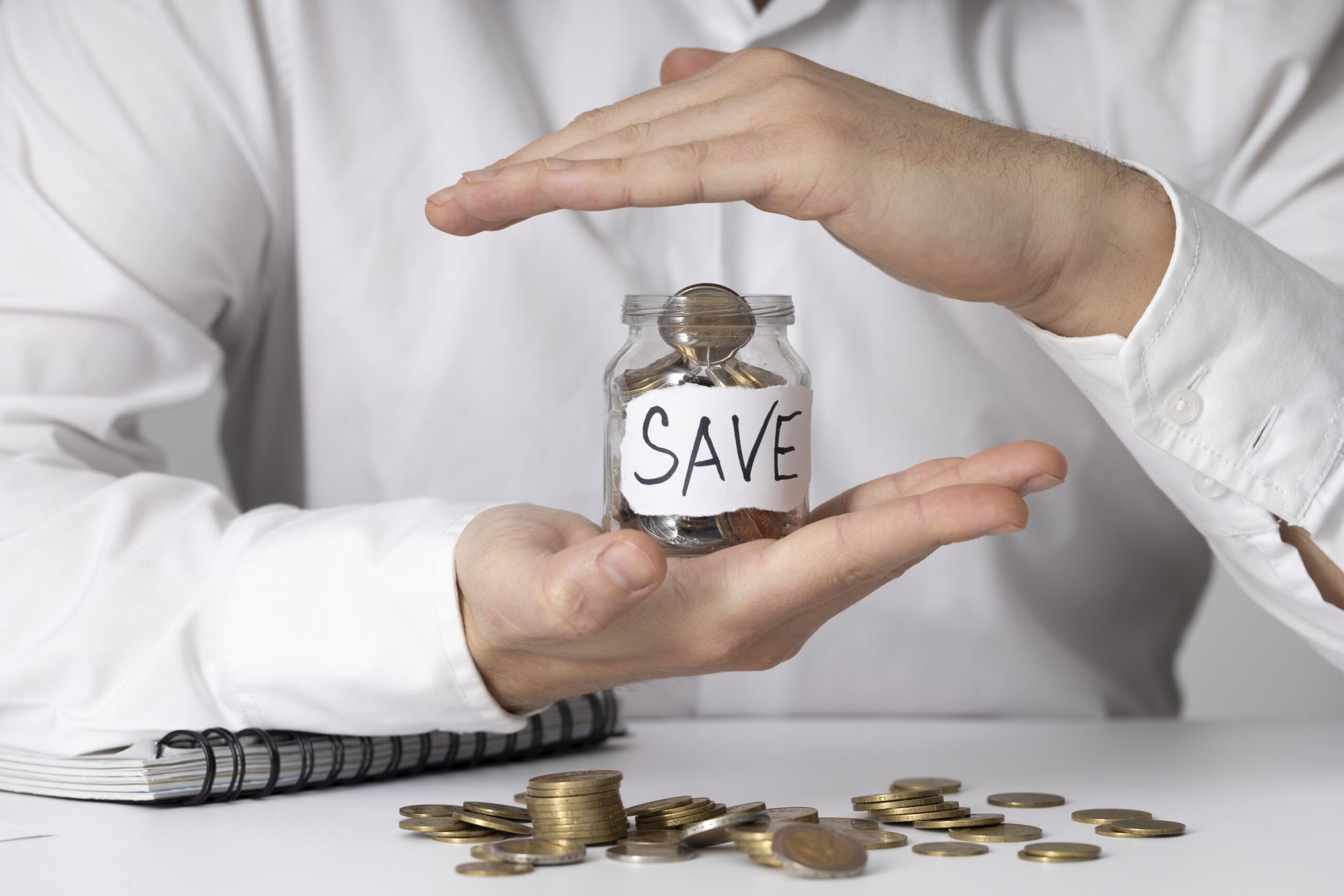
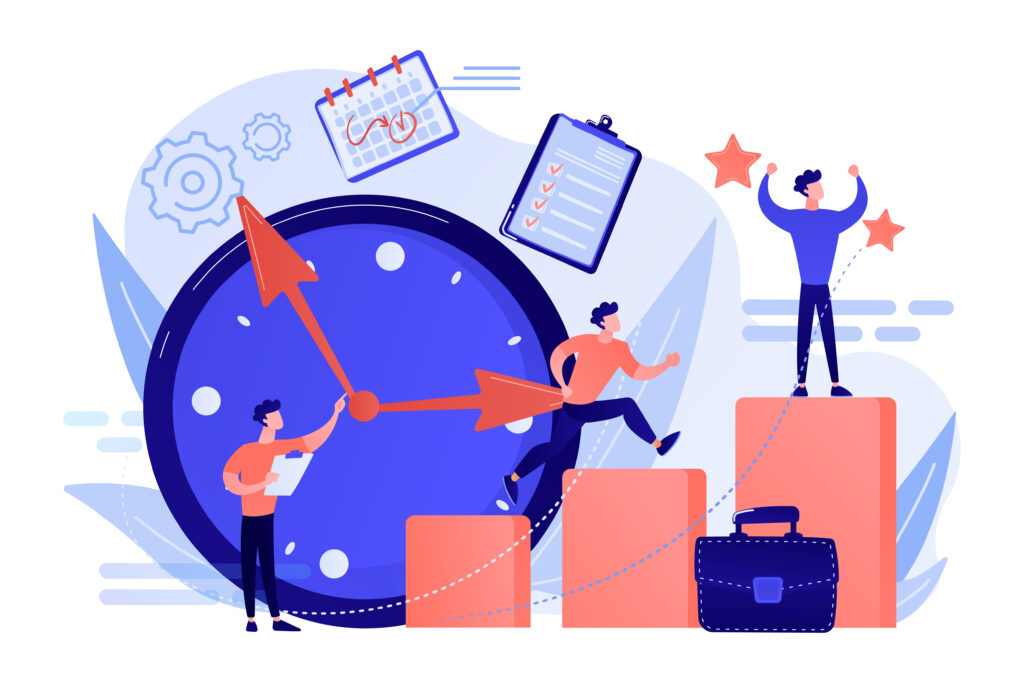
Productivity Enhancement
Increased productivity is the way towards increased production and optimization of the outcome. Everyone thus understands that in improving the organizational productivity we apply methods such as process improvement, utilizing technology, and implementing the best practices. So when you have a productivity issue, we assist in ensuring that factors that hinder operations are removed so that you may get improved efficiency.
Here’s how we do it
-
Lean Six Sigma
Lean Six Sigma is a fast and effective methodology that integrates the Lean process that deals with the minimization of waste and the deviation from the Standard Deviation focused by Six Sigma. Logicate Solution’s team of specialists applies Lean Six Sigma approaches to support your organizational processes, improve products, and optimize performance. Because we focus on the areas that need improvement, our presence automatically signifies tangible boosts in performance and buyers’ satisfaction.
-
Lean Manufacturing
Lean Manufacturing can therefore be described as the generation of increased value within the process of utilizing fewer resources. The steps that make up this strategy are to critically define your production activities to establish where and how waste occurs, and how resources can be better used to enhance the production systems of your manufacturing companies. aka consequently collaborates with your team to efficiently introduce Lean practice into the organization’s processes that will decrease lead times, improve product quality, and increase returns for your company.
-
Inventory Management
Stock control involves satisfying the demand of the consumers by ensuring that the organization has enough stocks to offer while at the same time ensuring that the cost of holding the stocks is kept as low as possible. We have specific stock management services with key components of forecasting, inventory, and supply chain management. Our strategies assist in the right stock being available at the right time, in minimizing the holding of unwanted stocks, in the right orders being placed, and in providing the right products to the right customers, at the right time.
-
Organization Restructure
Organizations with employees adapt to the changes in the business, and this means that the structures must also change. Our organization restructure services are designed to meet the objectives of ensuring that your company’s structure is in harmony with your strategic plans. We examine the existing structure, assess its effectiveness, and make recommendations on the changes that need to be done. These are to address communication means, status, approval, and authority, as well as roles and responsibilities to build new proper growth and flexibility for development.
-
Business Process Re-engineering
Business Process Re-engineering (BPR) entails the fundamental redesign of the strategic business processes to radically enhance their output. Consultatively, we engage you to evaluate current business processes, analyze key constraints, and optimize the processes for better productivity, less expenditure, and better standards. With our BPR approach, your processes are certainly adjusted to the present and future needs of the business.
-
Total Productive Maintainance
TPM stands for Total Productive Maintenance; a strategic maintenance approach focused on achieving equipment outputs without any failure in its productivity. TPM makes all employees participate in the process meaning that every employee has the responsibility of maintaining the asset. The main ideas include predictive, condition-based maintenance; Autonomous; and Mura, the Japanese term for ‘non-value-added’. Through TPM, equipment must be inspected frequently; breakdowns repaired swiftly; and operators trained on how to use the equipment most efficiently. This approach not only increases productivity and reliability but also decreases costs that are connected with the failures and repairing of equipment and technology resulting in increased efficiency and economic outcomes of the organization.
-
Factory Layout Design
It is also very vital to understand that the factory layout of your business can affect the function and productivity of the production system. Our factory layout design services involve designing a layout to encourage the effective flow of goods and other materials, curb wastage, and also the efficient use of space. Some of the aspects that we take into account include the circulation of products, position of tools, and safety to come up with layouts that enhance production and embrace the goals of your business.
Keep Your Business Safe & Ensure High Availability.
Lean Six Sigma is a business improvement approach which affinity incorporates Lean which underlines the elimination of the inefficiencies and Six Sigma which concentrates on the reduction of variation and enhancement of the product quality. Businesses derive advantage from the fact that it makes operations efficient and of higher quality, makes a business produce better outputs, and costs less while satisfying the customers more.
Lean Manufacturing is a business model that seeks to deliver more value to consumers through the use of fewer resources where the requirement for resources that do not create value is considered and removed or reduced. This results in cutting down on lead time, better quality, and hence improved profits.
Optimization of stocks involves ensuring that the overall stock levels are reasonable in as much as it eliminates high carrying costs while ensuring that the required products are available in stock at the right time. This in a way reduces the likelihood of stockouts and overstock, increases order precision, and increases customer satisfaction.
A possibility of changing your business’s hierarchical model could enhance productivity, collaboration, and supply change. Organizational developments make your company’s structural foundations reflect strategic plans, clarify organizational responsibilities, and facilitate decision-making processes for business growth.
BPR is a radical redesign of the business organization’s process to achieve overall improvements in performance. It encompasses process mapping that focuses on checking the current organizational processes, reviewing the points of congestion, and redesigning the process to improve efficiency and minimize cost.
Therefore, the factory layout means that workflow, stock and storage, space utilization, and other factors within a factory are improved, hence minimizing wastage. As it relates to the organization and layout of a production facility, it can enhance overall performance by taking into consideration the flow of the production process, location of equipment, and even safety measures; thus enhancing the brute output and providing lesser operational concerns.
Some of the tactics used to minimize cost include evaluating your costs with the view of making recommendations on how costs can be managed in other areas/facets. Thus, much attention is paid to optimizing the costs, excluding run-in expenses, while providing high-quality services.
Some of the aspects of productivity enhancement strategies include increasing the production line efficiency, technologies, and practices. This results in high operating efficiency, the least possible time out of order/repair, and all-around improved performance.